Ultra Sonic Cleaning
Ultrasonic Cleaning uses cavitation bubbles induced by high frequency pressure (sound) waves to agitate a liquid. The agitation produces high forces on contaminants adhering to substrates like metals, plastics, glass, rubber, and ceramics. This action also penetrates blind holes, cracks, and recesses.
BCS Inc. Has developed custom Ultra Sonic baths which exceed customers expectations.
All Ultra Sonic and High Purity Cleaning is done in our Clean Room.
- Automotive Parts
- Dental and Medical Equipment
- Surgical Equipment and Implants
- Steam Filters and Parts
High Purity Cleaning
BCS Inc is the industry leader in High Purity Cleaning for over 25 years. Our chemical cleaning procedures and high quality service ensure our customers equipment is operating to the demanding cleanliness levels set in place by the F.D.A.
BCS Inc have developed superior procedures and chemistry to ensure the safest, cleanest work environment for our employees and customers facilities.
To learn more about how BCS Inc can create a customized passivation plan to address your equipment and facility contact BCS Inc today.
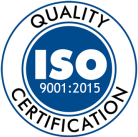
BCS Inc offers High Purity Cleaning to many systems and parts, some include:
WFI, HWFI, PW, DI, RO Piping and Tanks
Autoclave/Steam Sterilizer
Bioreactors
CIP + SIP Systems
Clean Steam + Pure Steam Generators and Piping
Production Equipment
Fermentors
Lyophilizer/Freeze Dryers
Gas/Nitrogen Piping
Medical Equipment
Vessels and Tanks
Product and Process Lines
We are happy to introduce an extension on our facility. We are developing new cleanrooms and laboratories to meet FDA and ISO standards.
High Purity & Precision Cleaning is offered both In shop and at our customers facility.
Contact Us today.
Media Blasting
BCS Inc has helped customers find the perfect stainless steel surface finish for any application needed. BCS Inc is partnered with numerous media blasting companies which allow us to determine the highest quality surface finish needed.
Specializing in small parts, BCS Inc has enclosed dry + wet media blasting booths.
Contact us today for any stainless steel surface preparation needs.
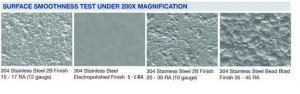
Inspection Services
BCS Inc is thoroughly involved with testing and inspections. Offering a Preventative Maintenance Program we diagnose customers systems with state-of-the-art inspection equipment. With quality documentation we pride ourselves on thorough inspection reports and solutions to internal + external surface corrosion.
We take pride in providing our clients with a non-destructive evaluation process. Our team offers flexible + rigid video borescope inspections.
Certified Inspectors with over 10 years experience. CWB Certified. VT.
Borescope is a specialty instrument with a flexible tube, which contains a camera at the end. We use the tube to navigate tight spaces. Our borescope inspection services can reveal potential problems that may result in collateral damage. Using the highest quality equipment available, our experienced team provides comprehensive borescope services with minimal unit disassembly.
Clean for Oxygen Services
BCS Inc is the industry leader on Oxygen Precision Cleaning. We have developed procedures and systems which meet standards ASTM G93. We have been in the Oxygen Cleaning business for over 25 Years and have developed methodology by our research and extensive experience in thoroughly cleaning customers systems and parts.
Oxygen Precision Cleaning
Our state-of-the-art clean room and laboratories were custom built to meet the precise demands of oxygen precision cleaning. Quality Control is of upmost importance, with documents, packaging and solvent cleaning BCS Inc demands top quality in every aspect of Precision Cleaning.
BCS Inc standard cleaning process consists of pre-cleaning and precision cleaning. We have developed systems with various wash and rinse stations. Ultrasonic baths, recirculating baths, detergent, and de-ionized water. Once washed and rinsed, parts are dried and purged before packaging into certified-clean primary and secondary bags. All cleaning processes can be customized with requests from customers to meet specific needs.
BCS Inc is capable of meeting oxygen cleaning specifications in standards such as ASTM G93, ISO 15001 EIGA 33/06, SAE ARP1176, CGA 4.1, MIL-1330D, and more based on customer request.
Pickling & Passivation is the removal of any high temperature scale and any adjacent low chromium layer of metal from the surface of stainless steel by chemical means.
Example of good post-weld practice Where the steel has been heated by welding, heat treatments or other means, to the point where a coloured oxide layer can be seen, there is a chromium depleted layer on the surface of the steel underneath the oxide layer. The lower chromium content gives lower corrosion resistance. To restore the best corrosion resistant performance, the damaged metal layer must be removed, exposing a fully alloyed stainless steel surface. Mechanical removal may leave abrasive or other particles embedded (interfering with corrosion performance) or may be impractical, so chemical means are usually employed.
Procedures incorporating pickling solutions of nitric (HNO3) and hydrofluoric (HF) acids remove the scale and the underlying chromium depleted layer and restore the corrosion resistance. Pickling solutions also remove contaminants such as ferrous and ferric oxide particles. Pickling solutions other than mixtures of nitric and hydrofluoric acids exist and can be used for specialized applications.
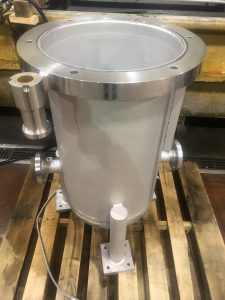
Rouge is a naturally occurring phenomenon in existing stainless steel high purity water systems such as water for injection, pure steam and ultra pure water stills, tanks and piping.
Rouging is an ongoing maintenance issue for pharmaceutical companies that operate stainless steel systems with steam or high purity water running at elevated temperatures. The combination of high temperature and pure water/steam will often allow the formation of iron oxides that proliferate throughout the systems in question creating a reddish layer on the surface of the stainless steel. There may also be an organic layer that forms on top of the iron oxide to make removal more difficult. If left alone the contamination may grow to such a level as to allow sloughing off of the iron oxide into the water stream and may also start to pit the surface of the stainless steel. The surface corrosion may eventually contribute to increased microbial contamination and further deterioration of the stainless surface.
Rouging may occur but not limited to these systems:
- Pure Steam Generators (PSGs)
- Steam Piping Systems
- Hot WFI Systems
- Hot PW Systems
- Production Systems
- Vapor Compression stills
- Autoclave – Sterilizers – Steam Ovens
The American Society of Mechanical Engineers in their paper: ASME BPE B31.1-2016 describes rouge as having three (3) Classes:
Class l ROUGE:
Weakly attached to the surface and easily removed and dissolved. This rouge is generally hematite and red ferric iron oxide with low levels of other oxides or carbon content
Class ll ROUGE:
This rouge consists mostly of hematite or ferric oxide with some amounts of chromium and nickel oxides as well as small carbon content. Class ll rouges are more difficult to remove than class one, and may require additional time to remove.
Class lll ROUGE:
Is much more difficult to remove compared to Class l and Class ll rouge, both due to its chemical composition difference and its structural differences. These high temperature deposits form magnetite iron oxide with some substitution of chromium, nickel, or silica in the compound structure. Significant amounts of carbon are generally present in these deposits due to reduction of organics present in the water, which sometimes produce the “smut” or black film that may form during derouging.
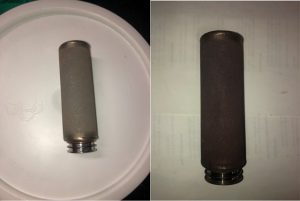
Electro Polishing
is a “reverse plating” process that uses an electrochemical solution to remove the outer skin of a metal part. …Electropolishing stainless steel significantly improves a part’s corrosion resistance, leaving it with a lasting bright finish.
Some Industries that use electropolish:
- Dental, Medical and Orthopedic Equipment
- Aerospace Equipment
- Bio Pharmaceutical
- Food Processing
- Food and Beverage
Common Parts that are electropolished:
- Stainless Steel Pump Parts
- Springs, Nuts + Bolts
- Fittings + Piping
Why Electro Polish?
The electropolishing process may improve a surface finish by up to 50%. The electropolishing reaction removes material while it improves surface roughness. Because of the material removal, process runtimes are often limited to maintain dimensional tolerances.
How is electropolishing done?
Electropolishing is an electrochemical finishing process that removes a thin layer of material from a metal part, typically stainless steel or similar alloys. The process leaves a shiny, smooth, ultra-clean surface finish. … Both are non-mechanical, chemical processes, but only electropolishing uses electrical current.
What is the difference between electropolishing and passivation?
Passivation is a chemical process designed to remove free iron and other contaminants from the part surface. Electropolishing is an electro-chemical process that removes surface metal which improves micro finish, provides deburring and adds to the aesthetics of your part.
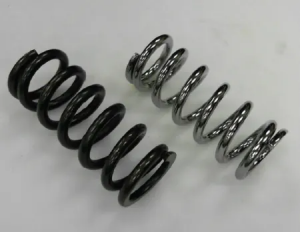